
“And this…” says the compact and impeccably dressed form of Holden’s head of design, Richard Ferlazzo, “…is our modelling studio.” He pauses for a moment, as though for dramatic effect, before pressing his security pass to the door to reveal a top-secret design studio that looks, well, exactly like you imagine it would.
Bright and open, with softly diffused light and a laid-back ‘creative vibe’ (all that’s missing are some beanbags and a ping-pong table), its focal points are three full-sized clay models that sit on axle stands at even intervals around the large room.
Around them mill a handful of casually dressed designers, their heads tilting and turning like inquisitive birds as they step back to take in new perspectives of their creations.
But it’s the clay modellers (or ‘clay sculptors’ as some like to be called) who we’ve come to see. They’re easy to spot, these masters of muck, these titans of terracotta – just look for the clay-caked fingernails.

Yet they’re also exceptionally easy to dismiss. Surely, in this digital age of computer-aided design (CAD), of 3D printers, and of virtual reality headsets, the need to use thousands of kilos of clay and to spend thousands of hours carefully crafting full-sized models out of mud is now largely irrelevant? It’s all a little ‘old school’, isn’t it?
Suggest such a notion to Ferlazzo, and he smiles and then shakes his head.
“It is remarkably low-tech…” he concedes. “But that’s what makes it so effective. People often ask me, ‘Okay, it’s 2019, you’ve been using clay for many, many decades (for reference, Holden has been making clay models since the 1940s), surely there’s a better way to do things?’. And for some parts of the design process, we do use modern methods, but for making full-scale models, clay is still the most suitable material.”
Holden’s Australian design team has grown to around 130 heads since the closure of local manufacturing, 25 or so of whom are clay modellers. And Holden isn’t alone here.
Peek behind the curtains of any design studio in the world and beyond the rows of enormous computer screens and software-guided milling machines, you’ll always find a core unit of highly skilled sculptors, each busily crafting a new line, curve or character point into a scale or full-size clay model.

“Clay modelling will always be important,” says Gorden Wagener, the head of Mercedes-Benz design and our #1 most influential designer. “We can do a car completely on a computer, but does it make sense? No. I’m a true believer in clay models.”
Even Tesla, a company infamous for its rejection of traditional methods, continues to use clay to breathe life into its new models.
All of which begs the obvious question of why? Why is clay still the go-to product? And how has such a simple and old-fashioned endeavour been able to retain its place at the centre of what is now a truly modern and digitised design process?
“The best thing about clay is that it’s both additive and subtractive,” says Ferlazzo. “And that makes it fast and easy. People say, ‘Why don’t you just 3D-print a model?’ We can, of course, but the problem with that is once you print it, you can’t alter it. You spend a lot of money printing it, which takes a long time, and then the only way to alter that model is to add a hard material like filler.
“With clay, you can think, ‘That part just needs a small revision’, so you whack on some clay to make the change, scan it digitally – which only takes about an hour and a half, to scan an entire car –and then you have an outcome that’s closer to perfection.
"Designing a car is a linear process but it’s also an iterative one with countless changes from design and engineering, so we’re constantly evolving the model. Clay lets us do that and keep engineering in the loop.”
We should clarify here that this ‘clay’ isn’t the same kind of clay you’ll dig up in your backyard, or find in art schools. In fact, it isn’t really clay at all.
Built to closely guarded, proprietary recipes (“they won’t tell us exactly what’s in it,” says Ferlazzo with just a hint of frustration), the clay used by car companies is more like a high-tech Plasticine made up of waxes and other agents.

Holden sources its clay from companies in Germany and Japan and it’s relatively expensive, at around $13 a kilo. It’s also heavy. Even the term ‘clay model’ is something of a misnomer, as the clay only makes up the final few inches of the model (underneath they’re built on a rigid steel armature which is then built up with wood and Styrofoam), each one nevertheless caked in more than a tonne of clay.
“Combine that with the metal frame and a model weighs a good three tonnes,” says Ferlazzo. “We have to use electric jacks to lift them and move them around.”
And as for cost? In materials alone, a clay model is worth upwards of $200,000. Factor in labour and it can be double that.
The beauty of modelling clay, as opposed to other materials, is that it never truly sets. Stored in giant ovens at around 65°C, it does harden slightly as it cools but it never air-dries or cures, so models can be stored for years and then pulled out to be worked on when the time comes for a facelift.
Smaller components, such as lights, grilles and bumpers, can simply be changed or removed entirely and then replaced by fresh designs that clip straight into the metal frame below.
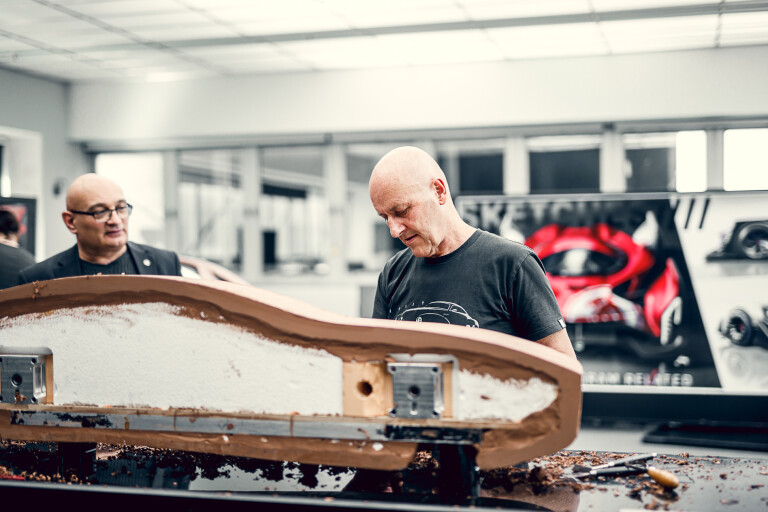
No-one truly knows who the first person was to craft a car from clay, though if you believe the legend, it all started with Harley Earl.
A design visionary and the man who revolutionised the look of General Motors’ cars over three decades from the early 1920s through to the 1950s, Earl used clay to convince uncertain customers and board members that his design vision could be trusted. Clay models were able to communicate his ideas in ways that sketches simply couldn’t.
That logic still rings true today. Producing full-size models and then allowing the design team and company executives to view them outside – usually in some secret internal courtyard (Holden’s has its own turntable) – is a crucial part of the process.
Paul Larkin has been a clay sculptor for more than 30 years and says that a model’s ability to communicate a car’s essence to upper management is vitally important internally.
“If a director from Cadillac comes to Australia to see how a new model is coming along, they go straight to the clay model – they don’t go to a screen,” he says. “We push it outside and they have the conversation about it in the real world.”
And it’s here that we get to the true differentiator between clay models and designing a car solely with CAD. Where computers are able to build a car from scratch, what they can’t capture are those intangibles that set the great designs apart from the merely mediocre.
The subtlety of a curve; the tension of a surface. Without that creative spark and the nuance of human touch that comes from clay modelling, designs taken purely from CAD tend to look wooden.

“The surface of a vehicle really is sculpture and it’s almost impossible to capture that entirely from a sketch or on a computer screen,” says Ferlazzo. “This is a large object, you really need to walk around it, to interact with it and see the way the light hits the surfaces, to understand that interplay of light and mood. You can build a car without a full-size model but if you leave it out, and miss that last bit of artisan finesse, then that just leads to mediocrity.”
There’s something strangely comforting about the knowledge that even in today’s digital world, there are still things only a human hand can achieve. And in that process, it’s the hands of the designer and the sculptor that are equally important.
Where a designer is responsible for a car’s overall look and feel, it’s the clay modeller that has to interpret the designer’s sketches and turn them into a 3D object. And it’s that synergy, and the level of understanding inherent in such a creative relationship, that can make or break a project.
“Sometimes it’s quite easy to mistake a divot for a bump and I’ll say to the designer, ‘Oh sorry, mate, I read that backwards, your shading wasn’t that good’,” says Larkin. “So the fact is, they rely on you and we rely on them. But they’re quite happy for us to have a go if we get stuck, and they’ll often say, ‘Oh that’s even better than I imagined it’.

“And if we reach a problem or something that’s not quite working, the beauty is we can simply scan where we’re at, then it doesn’t matter if we mess it up because we can just re-mill it again from clay. Modelling isn’t destructive. We still have to respect the designer because it’s their sketch, but that’s why clay is so great. It’s for experimenting.”
And, reassuringly for Larkin and his fellow sculptors, it seems his profession is one of the few in the automotive space that has a decent degree of job security.
“Clay will certainly be around for the remainder of my career,” says Ferlazzo. “There are people outside the industry who think it’s old school and dated, but those who use it, we know how important it is. I still haven’t seen an alternative that is any better.”
Beauty that’s skin deep
Clay models can look freakishly realistic. “From a distance, you can’t pick a clay from a production car,” says Richard Ferlazzo. “We even used to create models with real glasshouses, built around metal frames for an even more realistic finish.”
Models can be coated with primer and painted, though the more common practice is to cover the exposed clay with a proprietary material such as 3M’s Di-Noc. “Silver is the industry norm and it’s like wallpaper,” says Ferlazzo. “You put it in a water bath and it goes like cling wrap, then it hardens as it dries.” High-tech foils and 3D-printed door handles and alloys complete the illusion.
COMMENTS